Introduction
Increasing numbers of new cars are equipped with Advanced Driver Assistance Systems (ADAS). Some of the more common ones include:
- Forward collision warning
- Automatic emergency braking
- Adaptive cruise control
- Lane departure warning
- Lane keeping assist
- Blind spot monitoring
- Rear cross traffic alert
- Parking assist/self-parking
- Adaptive headlights that steer with the vehicle
- Automatic headlight high-beam activation and dimming
Figure 1. Typical ADAS sensors. LIDAR is not yet used in production vehicles. (Image: Texas Instruments)
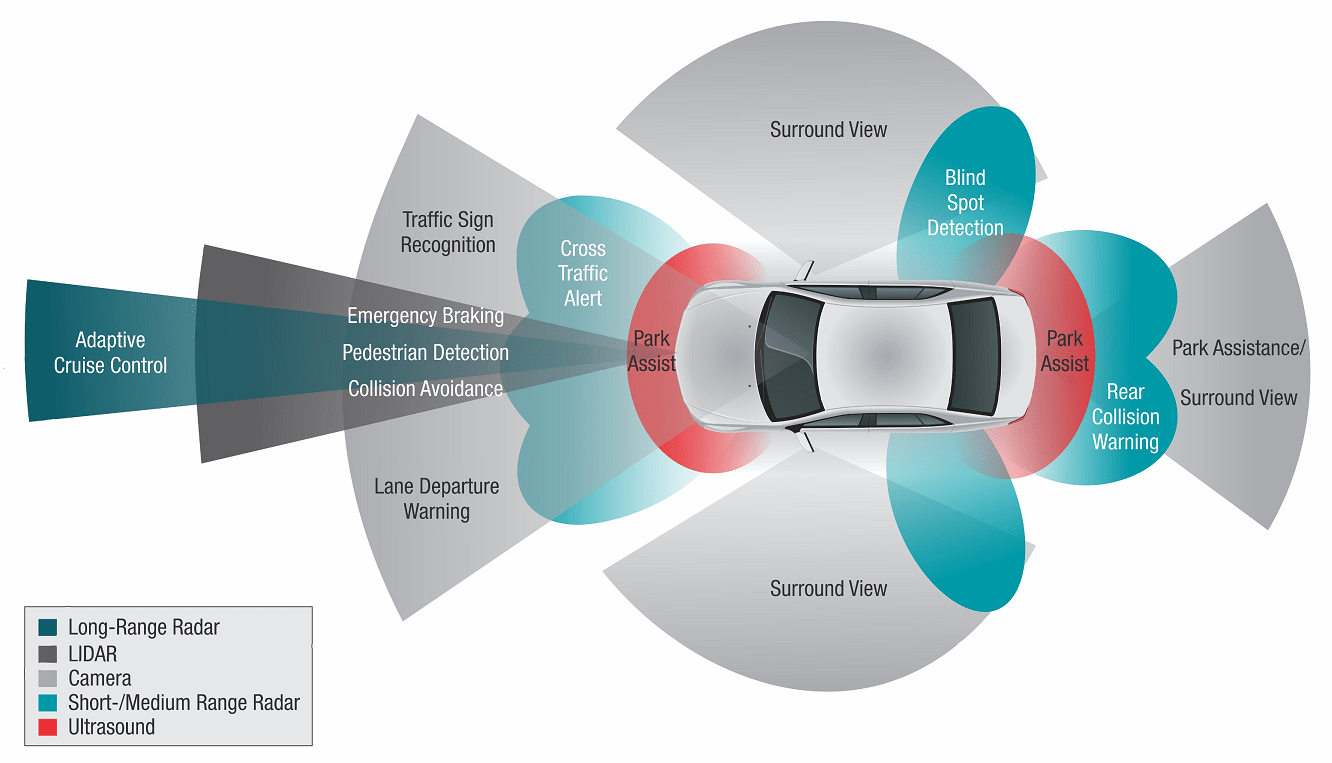
To do their jobs, ADAS rely on inputs from a variety of sensors that allow the systems to “see” what is happening around the automobile. The most common are camera, radar and ultrasonic sensors. Steering sensors are also used to help determine the direction of vehicle travel. Some systems use information from a single type of sensor, but others combine information from multiple sensors – a process called sensor fusion – to obtain a more accurate “view” of the situation.
Most ADAS sensors are very precisely aimed and require calibration if their positions are disturbed in any way. Consider that a sensor on the car that is out of alignment by a fraction of an inch or even one degree will be aimed at an area significantly off axis 50 or more feet down the road. Misaimed sensors often result from collisions – even a minor fender bender can knock ADAS sensors out of alignment. However, calibration can also be required as a byproduct of common car service work such as windshield replacement, suspension repair or wheel alignment.
Failure to calibrate a sensor when necessary can result in faulty information that will cause ADAS to operate improperly or not at all. Faulty sensor input can cause:
- A warning light or message on the instrument panel
- A diagnostic trouble code (DTC) being stored in the vehicle’s computer memory
- Steering wheel vibration
- Vehicle steering pull
- Increased steering effort
Problems like these can cause a driver to lose trust in a car’s ability to provide safe transportation. ADAS failures may also raise questions about the quality of an auto repair shop’s work.
Sensor Types
The most common types of ADAS sensors are cameras, radar units, ultrasonic transmitters and steering angle sensors. Here is more information about each.
Front-Facing Camera Sensors
Many vehicles are equipped with front-facing camera sensors. These sensors are commonly used for automatic emergency braking, adaptive cruise control, lane departure warning, lane keeping assist and automatic headlight high-beam activation and dimming.
Figure 2. Subaru's dual ADAS camera system. (Image: Subaru)
Because cameras are optical devices that must be able to “see” the road, it is usually easy to identify when a car is equipped with this type sensor. Many camera sensors mount against the inside of the windshield as part of an assembly integrated with the rearview mirror; others attach to the inside of the roof – either directly or as part of a mirror housing. Some automakers, including Subaru and Land Rover, use dual cameras spaced apart from one another to provide enhanced depth perception.
The high-definition image receptors used in camera sensors are not all that different from those found in other digital camera applications. What makes ADAS camera sensors unique is the high-powered microprocessors and advanced data processing algorithms that are built into the assembly. These components turn the constantly changing analog image the camera sees into digital information that ADAS can use to control various safety-critical systems.
Camera sensors “see” the world through the windshield, and are designed for specific rates of light transmission through glass that has minimal imperfections and distortion. A problem in any of these areas can interfere with a sensor’s ability to provide accurate information. Because of this, many automakers specify that only an Original Equipment Manufacturer (OEM) windshield be used if replacement is necessary on a car with a camera sensor. In fact, some car dealers will refuse to calibrate a camera sensor on a car that has an aftermarket windshield installed.
Other Camera Sensors
Some newer cars have 360-degree “around-view” camera systems that use several small cameras at the front, rear and sides of the vehicle to display an overhead view of the immediate area around the vehicle. These are simpler and lower-resolution cameras than those used for ADAS, although they also require calibration. The cameras are usually located in the front bumper or grille, under the side mirrors, and in the trunk lid or liftgate. The computer controlling the system “stitches” the multiple images together to provide a smooth overall view displayed on the infotainment screen in the dash.
Front-Facing Radar Sensors
Adaptive cruise control, forward collision warning and automatic emergency braking are the ADAS most commonly associated with front-facing radar sensors. The millimeter wave radar sensors used on vehicles transmit a high-frequency radio signal that reflects off objects and returns to the sensor. The time it takes to receive a return signal is used to calculate the car’s distance from an object.
Figure 3. This "see through" image shows how a radar sensor may be positioned behind a solid plastic cover in the grille. (Image: Mercedes-Benz)
Because they are sometimes hidden, determining whether a vehicle has a radar sensor can be more difficult than identifying the presence of a camera sensor. If an external visual inspection does not indicate the presence of a sensor, opening the hood could reveal one. Another method is to check for adaptive cruise control switches inside the car (usually on the steering wheel) or a warning light for an automatic emergency braking and/or adaptive cruise control system that illuminates on the dash as a test when the car is first started.
Other Radar Sensors
Some rear collision warning and blind spot monitoring systems use small radar sensors mounted under the side view mirrors, behind the rear bumper cover or even in the taillights. Bumper- and taillight-mounted sensors may also provide rear cross-traffic alerts when backing out of parking spaces.
To prevent potential interference, most auto manufacturers do not allow repairs to areas of bumper covers that are in front of radar sensors. They also recommend the use of only OEM covers to ensure that the materials used will not interfere with the sensor signals. Excessive bumper cover paint thickness can also be a problem on some vehicles, and automakers advise against placing bumper stickers anywhere near the radar sensors.
Ultrasonic Sensors
Ultrasonic sensors are primarily used for parking assist and self-parking systems. These sensors are installed in the front and/or rear bumper covers where they use reflected high frequency sound waves (in a manner similar to radar) to detect people, cars and other objects in close proximity to the vehicle. Sensors of this type on the sides of cars are used in some self-parking systems and may serve as supplemental sensors in blind-spot monitoring systems.
Figure 4. An ultrasonic sensor on the edge of a wheel well opening. (Image: Wikipedia, Basotxerri, CC BY-SA 4.0)
Steering Angle Sensors
Steering angle sensors are used in lane departure warning, lane keeping and adaptive headlight ADAS. The information they provide is also used for other safety and performance-related systems such as electronic stability control and adaptive suspensions. These sensors are usually built into the steering column and measure the degree of steering wheel rotation.
Sensor Calibration
ADAS sensor calibration is required whenever a sensor’s aiming is disturbed in any way. This can occur in a collision, even a minor fender bender, or be a byproduct of common service work such as windshield replacement, suspension repairs or wheel alignment. Calibration is also called for whenever a sensor or its mounting bracket is removed and replaced, there is a change in tire size, a front airbag deploys and deflects off the windshield, or repairs are made to a car roof that has a sensor bracket mounted to it. Finally, sensor calibration is necessary when there is a related DTC in the car’s computer memory, or an automaker releases a technical service bulletin with instructions that calibration be done as part of another repair.
Sensor replacement and calibration are frequently part of collision repairs. Automakers recommend that body shops now perform a complete diagnostic scan on every vehicle before repairs are begun, and then again after the job is complete. Doing so will help the auto body shop better understand the scope of any problems before work starts, and then confirm that all issues have been resolved, ADAS sensor calibrations are complete, and the vehicle control systems are communicating properly before the car is returned to the customer.
Figure 5. An aftermarket multi-function automotive diagnostic scan tool. (Image: Snap-On)
Shop Preparation
Because of the challenges involved, many auto repair shops and windshield installers currently send cars to the dealer when ADAS sensor calibration is required. Independent service providers that want to perform sensor calibrations must make a significant investment in these necessary tools:
- Service information that describes the equipment and procedures required to calibrate the ADAS sensors on any given year, make and model of vehicle. This information may be available from the aftermarket, but sometimes must be obtained from the auto manufacturer. ADAS sensor calibration requirements can be determined by performing an OEM Calibration Requirements Search, or by using links to OEM service information. Both options incur a cost for the servicing shop.
- A car computer scan tool that supports ADAS sensor calibration. Factory scan tools can handle the necessary operations for all vehicles and sensors from a specific automaker. Aftermarket scan tool capabilities vary widely, but certain devices will work with some vehicles and sensors from a number of different automakers. Special tools designed exclusively for ADAS sensor alignment are also available, but as with aftermarket scan tools the extent of vehicle coverage varies.
- A large, level, paved, indoor area with non-glare lighting and a backdrop free from clutter (camera sensors) and metallic objects (radar sensors) that can interfere with calibration. Honda, for example, specifies an open area that is 13 feet wide, 5 feet high and extends at least 23 feet in front of the car. The Lexus radar calibration process (done outdoors) requires a large, level open road at least 32 feet long and 45 feet wide ahead of car.
- A wheel alignment rack. Many automobile manufacturers require or recommend that a four-wheel alignment be performed prior to ADAS sensor calibration. This ensures that the vehicle thrust line, an imaginary centerline drawn lengthwise through the car, points straight down the road when the steering wheel is centered. ADAS sensors are then calibrated to be in alignment with the thrust line. Wheel alignment equipment is now becoming available with built-in ADAS calibration capabilities, although a static and/or dynamic aiming process (see below) may still be required.
Figure 6. A dedicated tool for ADAS camera sensor calibration. (Image: Pilkington)
Vehicle Preparation
Prior to calibrating an ADAS sensor, a vehicle must be prepared as specified by the automaker. Some of the common requirements include:
• No unnecessary heavy items in car or trunk
• Tires inflated to recommended pressures
• Front and rear vehicle ride height within specifications
• Fuel tank full
• Windshield clean in front of camera sensor (where applicable)
• Protective cover removed from radar sensor (where applicable)
• Four-wheel alignment performed (where specified)
Calibration Methods
There are two forms of ADAS calibration, static and dynamic. General descriptions of these processes are provided below, but the exact procedures vary significantly from one vehicle make and model to the next. In all cases, the automaker’s specified procedures and instructions must be precisely followed.
In-Shop (Static) Calibration
Static sensor calibration begins with establishing the vehicle thrust line. Automakers specify a variety of manual measuring methods and special tools to perform this part of the process. In many cases the tools attach to, or are aligned with, the front and rear wheel hubs. Laser projectors are often built into the tools to help ensure perfect alignment.
Next, one or more special aiming targets are positioned in precise locations relative to the thrust line and sensor. The targets must be at a specified height, and many are designed for use with special adjustable mounting stands. Where a sensor is offset from the car’s centerline, the targets must be correspondingly offset as well. While at least one vehicle uses a target that is placed on the hood, most target locations are 10 to 20 feet from the vehicle.
Camera aiming targets are usually black and white patterned images that are purchased or, in some cases, can be downloaded from service information sites. Targets that have been downloaded may have to be resized using a copy machine. With some vehicles, the target must be lighted in a specific manner to ensure proper calibration.
Figure 7. Typical ADAS camera aiming targets – VAG indicates Volkswagen/Audi Group. (Image: TEXA)
Figure 8. A reflective aiming cone for radar sensor calibration. (Image: Honda)
Figure 9. A horizontal leveling tool attached to a radar sensor. (Image: Nissan)
Following static calibration, many sensors require a follow-up dynamic process as described below. Even when a dynamic calibration is not required, a test drive is recommended to validate calibration and ensure that the ADAS do not set any diagnostic trouble codes when in operation. Some systems will not set DTCs or generate other error messages until the car has been driven a certain distance.
On-Road (Dynamic) Calibration
Dynamic sensor calibration is generally the preferred method for camera sensors, and sometimes the only method specified. Radar sensors, on the other hand, often require static adjustment followed by an on-road procedure. Dynamic calibration involves initiating the process with a factory scan tool, or aftermarket equivalent, and then driving the car on relatively straight roads with clear lane markings for 5 to 30 minutes at specified speeds until the scan tool indicates calibration is complete. On some cars, a warning light or message on the dash will go out when calibration has been successful.
Certain systems calibrate best when there is minimal surrounding traffic, but others will calibrate more rapidly when many objects are detected by the sensor. Vehicle manufacturer calibration instructions will provide information on the optimal process. Oftentimes, calibration cannot be done if rain or snow obscures lane markings, or other factors make it impractical or unsafe to drive at the required speeds.
Around-View Camera Calibration
Calibration of the around-view cameras is required when one or more cameras are replaced, or a mounting part (grille, door mirror, door, bumper cover, etc.) is removed and replaced. Around-view camera calibration is usually an in-shop static procedure. Large patterned mats are placed around the vehicle, and a factory scan tool is used to initiate the calibration process. Some around-view systems use an on-road dynamic process where the car is driven slowly down the road under very specific driving conditions.
Figure 10. A truck positioned between alignment mats used for around-view camera calibration. (Image: I-CAR)
Steering Angle Sensor Calibration
Calibration of the steering angle sensor may be required after air bag deployment, structural repairs or wheel alignment. The process normally involves placing the wheel in a straight-ahead position, and then using a factory scan tool, or aftermarket equivalent, to zero out the sensor signal.
Figure 11. Using a scan tool to calibrate a steering angle sensor. (Image: VDO)
Conclusions
There is no question that ADAS make driving easier and safer. However, the added complexity of these systems and their sensors comes with costs beyond their original purchase price. Just having a windshield replaced or a wheel alignment performed on a modern car with ADAS can be much more expensive. First, because any operation that alters sensor aiming calls for a time-consuming precision calibration procedure. And second, because the use of OEM parts, such as windshields and bumper covers, may be specified to ensure that the sensors acquire accurate data. These requirements can add to the cost of auto repairs, but must be observed to ensure optimum vehicle safety.
Finding Quality Auto Repair
AAA recommends that you plan ahead for vehicle service by finding an auto repair shop and technician you can trust before you need them. AAA.com/Repair provides information on nearly 7,000 Approved Auto Repair facilities that have met AAA’s high standards for appearance, technician training and certification, insurance coverage and customer satisfaction. AAA regularly inspects every Approved Auto Repair facility and surveys their customers to ensure ongoing performance. In addition, AAA members receive special benefits that include auto repair discounts, an extended 24-month/24,000-mile parts and labor warranty, and AAA assistance in resolving repair-related issues.
To Learn More
AAA SITES
AAA Exchange, Advanced Driver Assistance Systems,
http://exchange.aaa.com/automotive/automotive-trends/advanced-driver-assistance-systems
AUTOMAKER SITES
Subaru, Eyesight,
https://www.subaru.com/engineering/eyesight.html
Mercedes-Benz, Distronic Plus,
http://techcenter.mercedes-benz.com/en_AU/distronic_plus/detail.html
U.S. Environmental Protection Agency – Gasoline Standards,
https://www.epa.gov/gasoline-standards
TOOL SUPPLIER SITES
Absolute Alignment, Advanced Driver Assistance Systems and Vehicle Alignment,
https://absolutealignment.co.uk/.../Advanced-Driver-Assistance-Systems.pdf
Hella Guttman, Hella Guttman Movie CSC-tool-EN (video), August 5, 2014,
https://www.youtube.com/watch?v=CfK8G6WKQpA
Hunter, HawkEye Elite® Alignment Systems,
http://www.hunter.com/Portals/0/Media/6230-T.pdf
Hunter, Variety of OEM requirements for calibration could be hurdle for shops, March 28, 2017,
http://www.repairerdrivennews.com/2017/03/28/hunter-variety-of-oem-requirements-for-calibration-could-be-hurdle-for-shops/
Wikipedia – Gasoline,
https://en.wikipedia.org/wiki/Gasoline
Pilkington, Opti-Aim,
http://www.pilkingtonclearadvantage.com/opti-aim
TEXA, ADAS cameras calibration solutions (video), March 21, 2017,
https://www.youtube.com/watch?v=CvPRVnm9dMQ
INDUSTRY/PROFESSIONAL SITES
Autoglass, What is ADAS Windscreen Calibration?, October 10, 2017,
http://blog.autoglass.ie/adas-windscreen-calibration/
Glassbytes.com, Calibrations: What Technicians Need to Consider, May 25, 2017,
https://www.glassbytes.com/2017/05/calibrations-what-do-technicians-need-to-consider/
Glass.com, Windshield Replacement Calibration with ADAS: What You Need to Know, May 5, 2017,
https://info.glass.com/windshield-replacement-calibration-adas/
I-CAR, Typical Calibration Requirements for Blind Spot Sensors,
https://rts.i-car.com/collision-repair-news/typical-calibration-requirements-for-blind-spot-sensors.html
I-CAR, Typical Calibration Requirements of Forward Facing Cameras,
https://rts.i-car.com/collision-repair-news/typical-calibration-requirements-of-forward-facing-cameras.html
I-CAR, Typical Calibration Requirements for Forward Radar Sensors,
https://rts.i-car.com/collision-repair-news/typical-calibration-requirements-for-forward-radar-sensors.html
I-CAR, Typical Calibration Requirements for Park Assist Sensors,
https://rts.i-car.com/collision-repair-news/typical-calibration-requirements-for-park-assist-sensors.html
I-CAR, Typical Calibration Requirements for Steering Angle/Position Sensors,
https://rts.i-car.com/collision-repair-news/typical-calibration-requirements-for-steering-angle-position-sensors.html
The Windscreen Company, ADAS Windscreen Camera Calibration (video), February 6, 2017,,
https://www.youtube.com/watch?v=3JvJhvf0pic
Body Shop Business, Recalibrations – Are You Aiming in the Right Direction?, October 2017,
http://www.bodyshopbusiness.com/technical-recalibrations-aiming-right-direction/